Product Line
|
-
VEXTA®
|
Motor Type
|
-
Closed Loop
|
Frame Size
|
-
2.36 in60 mm
|
Motor Length
|
-
6.24 in.158.6 mm
|
Speed-Torque Characteristics
|
-
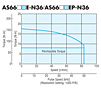 Speed - Torque Characteristics
|
Holding Torque
|
-
1120 oz-in8 N·m
|
Type
|
-
Standard
|
Shaft/Gear Type
|
-
Planetary Gear
|
Gear Ratio (X:1)
|
-
36 :1
|
Backlash
|
-
15
|
Feedback Device (Motor)
|
-
Resolver
|
Electromagnetic Brake
|
-
Equipped
|
Shaft
|
-
Single
|
Power Supply
|
-
Three-Phase 200-230 VAC
|
Current
|
-
1.5 A
|
Resolution
|
-
0.01 °
|
Resolution Setting: 1000 P/R
|
-
0.01 °/Pulse
|
Permissible Speed Range (r/min)
|
-
0 ~ 83
|
Rotor Inertia
|
-
3.1 oz-in²564x10-7 kg·m²
|
RoHS Compliant
|
-
Yes
|
Safety Standards
|
-
UL CSA EN CE
|
CE Marking
|
-
Low Voltage Directives EMC Directives
|
Insulation Resistance
|
-
[Motor] 100 MΩ minimum when measured by a 500 VDC megger between the frame-windings and frame-electromagnetic brake windings. [Driver] 100 MΩ when measured by a 500 VDC megger between the frame-power supply input terminal and I/O-Power supply input terminal.
|
Insulation Class
|
-
[Motor] Class B (266ºF [130ºC]), UL/CSA: Recognized as Class A 221ºF (105ºC)
|
Dielectric Strength (Motor)
|
-
Sufficient to withstand the following for one minute: Frame-Windings 1.5 kV 50 or 60 Hz, Frame-Electromagnetic brake windings 1.0kV 50 or 60 Hz
|
Dielectric Strength (Driver)
|
-
Sufficient to withstand for 1 min. - Frame-Power supply input terminal 1.5 kV 50 or 60 Hz, I/O-Power supply input terminal 1.8 kV 50 or 60 Hz
|
Ambient Temperature Range
|
-
[Driver] 32ºF ~ 104ºF (0ºC ~ 40ºC) [Motor] 32ºF ~ 122ºF (0ºC ~ 50ºC), nonfreezing
|
Ambient Humidity
|
-
85% or less (noncondensing)
|
Operating Atmosphere
|
-
No corrosive gases, dust, water or oil.
|
Components
|
-
ASD12C-SP (Driver) ASM66MCE-N36 (Motor)
|
Shaft Runout
|
-
0.002 in. (0.05 mm) T.I.R.
|
Concentricity
|
-
0.003 in. (0.075 mm) T.I.R.
|
Perpendicularity
|
-
0.003 in. (0.075 mm) T.I.R.
|
Permissible Overhung Load
|
-
0 in. from Shaft End = 74 lb0.2 in. from Shaft End = 81 lb0.39 in. from Shaft End = 90 lb0.59 in. from Shaft End = 101 lb0.79 in. from Shaft End = 117 lb0 mm from Shaft End = 330 N5 mm from Shaft End = 360 N10 mm from Shaft End = 400 N15 mm from Shaft End = 450 N20 mm from Shaft End = 520 N
|
Permissible Thrust Load
|
-
22 lb100 N
|